CCTV software applications
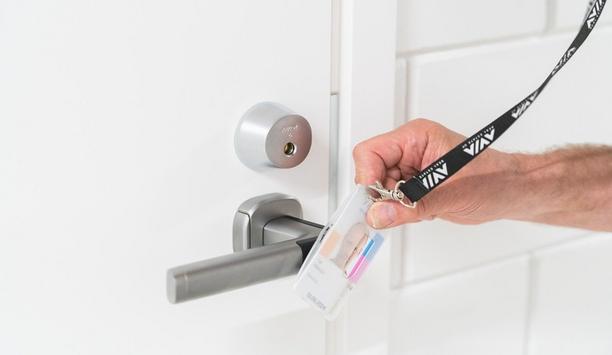
Managing access to and around Helsinki Airport is a complex task. Around 15,000 people work there daily pre-pandemic passenger numbers hovered around 60,000 to 70,000. Challenges faced Only authorised people should have access to many areas at an airport. The management of movement — by passengers, staff, and contractors— is critical to Finavia’s mission to deliver an efficient service. They sought new access solutions to help. Finavia staff and customer safety is paramount. In addition, every new access control device must: Facilitate the move to keyless security at the airport, which aims to enhance user convenience. Offer compatibility so Finavia can secure all types of openings, from doors and cabinets to fences and cargo. Integrate seamlessly with the existing access control system and software used at Helsinki Airport. Meet essential requirements for securing such a sensitive site: safety, functionality, durability and usability. Solution With Aperio H100 battery-powered handles, all types of airport doors are connected Partnering with ASSA ABLOY gave Finavia a vast choice of solutions to meet its complex security needs. With Aperio H100 battery-powered handles, all types of airport doors are connected to their access control system. This Aperio solution with inbuilt RFID capability was easy to install without the cabling that traditional devices require. “We see in real-time who will open the lock and when, and we can modify and grant access rights, remotely,” explains Kari Mäkinen. Programmable, secure ID cards Authorised building users come and go with programmable, secure ID cards. It’s much more convenient than a mechanical key, “The access cards of both Finavia personnel and staff of other companies are easily programmed with necessary access rights,” he adds. “When employees change, their access is disabled. Or if the card gets lost, it can be completely removed from the system. With mechanical keys, that process is much harder.” Durability, security of supply, and usability Multiple compatible ASSA ABLOY solutions are deployed alongside wireless Aperio and CLIQ door devices. Keyless, mobile-operated padlocks secure fencing and cargo. An antimicrobial coating on door handles helps to prevent germ spread and reassures staff. The availability of all these solutions from a single manufacturer helped Finavia to create a unified, integrated system at Helsinki Airport. “Safety, functionality, durability, security of supply, and usability were the reasons we chose the ASSA ABLOY solution,” said Kari Mäkinen, Senior Access Control Specialist at Helsinki Airport.
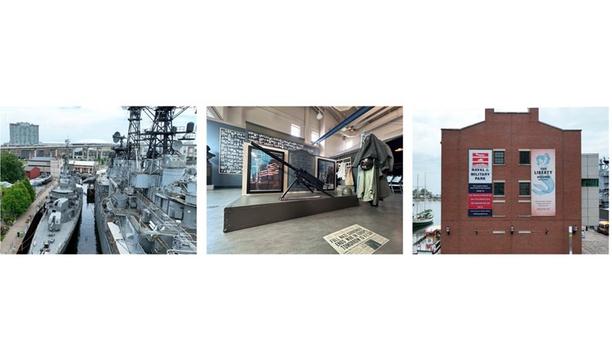
The Buffalo and Erie County Naval & Military Park, in Buffalo, N.Y., has a clear mission based on four pillars: to honour all veterans, educate the public about the sacrifices made by those who serve, inspire a sense of patriotism and appreciation for those protecting Americans’ rights and freedoms, and preserve the artifacts entrusted to the Park’s care. Buffalo Park The Park regularly hosts events and takes visitors inside America’s military history with in-depth tours of decommissioned naval vessels, exhibits, and displays. The team’s goal is to highlight its monuments and artifacts while providing a welcoming and secure environment for visitors. A key challenge was the Park’s large open and unfenced grounds, allowing the public access to the facilities at any time of the day or night. Challenge Provide a welcoming and secure environment for visitors and deter criminal activity within the park. Achieve 360° coverage across all interior and exterior areas without using cables, which would have made the project cost-prohibitive. Design a wireless surveillance system to cover the park’s large areas of open ground. Surveillance system installation “We had begun to notice an increased rate of delinquent incidents happening during the day and off hours, including graffiti placed on the artifacts and monuments,” said Paul Marzello, Sr., President & CEO, Buffalo and Erie County Naval & Military Park. The Park engaged Mario Rodriguez, president of Forseti Protection Group, and Erik Schiefer, account executive at Seibold Security, to design and install a surveillance system based on Hanwha Vision’s multi-directional and AI-equipped cameras. “When we did our research, we found that Hanwha Vision certainly was a pioneer in the industry,” said Marzello. Factors to consider From a risk and public safety perspective, the goal from the start was to maintain an open and welcoming environment “We conducted a site survey, considering the line of sight, the cameras’ capabilities, the density of groups of visitors and where they tend to gravitate, and criminal history in the Park,” said Bill Abbott, Director of Operations, Buffalo and Erie County Naval & Military Park. “Those were all factors in how we determined the layout. We wanted to make sure that we had the right coverage.” From a risk and public safety perspective, the goal from the start was maintaining an open and welcoming environment while keeping public safety top-of-mind. Solution Install a Hanwha Vision surveillance system comprising multidirectional and AI cameras. 4K multi-sensor cameras Schiefer has extensive experience with Hanwha cameras from previous projects. “Their new 4K multi-sensor cameras are first class and as far as 360° coverage, with the ability to monitor several areas, Hanwha was the first choice,” he said. The ability to view 360° coverage from one camera that essentially is divided into multiple sectors was significant. “That gives us full visibility and lets us be open and welcoming while keeping out of the public’s way without being imposing or intimidating,” Rodriguez said. Ease of playback Schiefer added that one key benefit of using the Hanwha 360° cameras to cover such a large area Schiefer added that one key benefit of using the Hanwha 360° cameras to cover such a large area is the ease of playing back footage and monitoring activity after the fact. “They are broken out into four sensors, so you don’t necessarily have to go back and look through a large amount of footage,” he said. “You can pick the area you're looking for, go directly to that sensor within the camera that we have in that area, and you can pull footage much easier that way.” Cable cost and distance One challenge the team encountered during the design phase was running a cable for a project of this scale. “The cost to run buried cable at such long distances with switches would have rendered this project almost completely impossible,” Schiefer said. “We incorporated wireless network cards into the poles around the park and all the cameras feed directly back to the Hanwha NVR without using any sort of cabling.” NDAA compliant solutions The Park’s priorities included the use of National Defense Authorization Act (NDAA) compliant solutions and having more streamlined communication with law enforcement. “We wanted to make sure that the cameras themselves were secure,” said Abbott. “The cameras also needed to be used to positively identify someone who had done something, either damage or acts of violence. In the past, we could not effectively supply law enforcement with usable information to identify a suspect." Use of AI in cameras The Hanwha cameras’ use of AI plays a key role in delivering those capabilities "We've now changed that with the quality of cameras that we're using. We can share footage and data to produce an outcome that's satisfying to everybody as far as finding a culprit and holding them accountable." The Hanwha cameras’ use of AI plays a key role in delivering those capabilities. “You can use key identifiers, whether it's the colour of someone's shirt, if they're wearing a backpack, or there's some physical feature that we can then go through and locate that person through the system,” Abbott said. Sense of security “We absolutely would see an increase in the value and number of cameras that we use,” said Abbott. Marzello added, “From an operations standpoint, we feel a greater sense of security knowing the cameras are there and will help us identify activities that we can hopefully prevent. This system meets our needs today and will also be able to grow with us.” Results Ability to effectively monitor all park areas and more effective forensic searches. Reduction in on-premise incidents. Streamlined collaboration with law enforcement agencies.
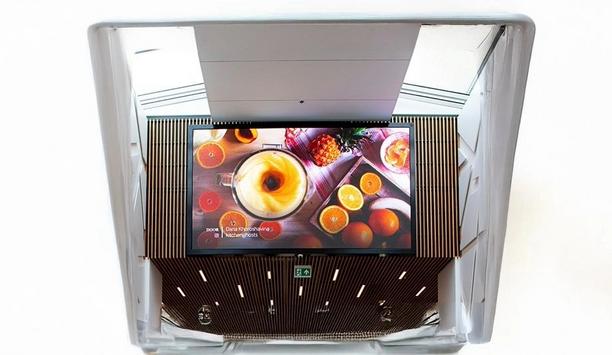
About a year and a half ago, Peter de Jong introduced Dahua to Fred Koks, General Manager of KITT Engineering. Since then, Dahua, KITT Engineering, and Ocean Outdoor have completed five joint projects. Follow-up appointments for the next two projects are already scheduled. Looking back "Let's see what happens" was Fred's reaction when introduced to Dahua. ''We evaluate our portfolio with suppliers every year,'' he explained. "We have to. So much is changing and new technology is developing incredibly fast. You have to keep up." He knows better than anyone how mobile the market is. "Among suppliers of LED screens, there is a constant battle for market position and new technology. We all know the big providers and the market pioneers. But it is not necessarily that they are also at the forefront of technology." Working in collaboration Erwin van Domselaar, Operations & Project Manager at Ocean Outdoor, says his company dares to blindly trust the expertise of Koks and his people when choosing a particular type of LED screen. "KITT Engineering is our technical supplier. They are very good at distinguishing good products from bad ones, and we trust them completely. When they have a product they see a future in, they discuss it with us to see if we can take on a project together with it." Shopping centre - Koperwiek In Dahua's case, that first project is a screen in a shopping centre called Koperwiek – an indoor shopping centre with more than a hundred fashion-related shops – located in Capelle aan den Ijssel. "That was a relatively small project," Erwin recalls. "The screen was not too big. But the initial learnings and experience with the screen were very good before we started. And the installation itself went off without a hitch. Exactly what we expected from this product." Shopping centre - Sterrenburg Soon, a second project was launched. This time in a shopping centre called Sterrenburg in Dordrecht. "Here, not everything went smoothly right away. Not regarding the screen, but its coincidence with the shopping centre's renovation. They had just finished." "All the walls had been neatly plastered and at that moment we asked if a new cable could be drawn. Fortunately, all this was eventually dealt with and solved in a very pleasant cooperation with the project developer, but it took some time." Pure craftsmanship The third and fourth projects are true masterpieces. In Hoofddorp, KITT Engineering installed a corner screen. "A unique screen for us," says Erwin. "It is the first screen that goes around a corner. It is half a meter that goes around the corner, fitting in super nicely with the surroundings." "On paper, a huge screen of forty square meters, but when you stand there, you don't notice it because it blends in so well with the surroundings. We are always looking for something new and surprising. And a screen that turns around the corner offers a lot of new possibilities. For example, in terms of 3D content." The screen turns around the corner Fred adds, "The screen doesn't just go around the corner, it goes around the corner seamlessly. KITT is always trying to bring novelties forward so we've had corner screens before. But that was in art projects and things like that where requirements are a lot lower." "In the process, we were able to try out various techniques and we also found out that the products we had at our disposal at that time were not one hundred percent ready." Cold corner "Then Dahua came up with a prototype, we were very pleased with the 'cold corner' as we call it. It is LED on LED, without a seam." To understand how clever this feat of engineering is, it's worth realising that the margin you have to make the image seamless is the space between two LEDs. Millimeter work, on a length of ten by five meters. Zuidplein shopping centre "The fourth project was placing a screen in the atrium of Zuidplein shopping centre in Rotterdam," Peter says. "The screen was placed against a glass elevator." "When you see that, [it is] not normal the way it came together. You don't see a cable or anything. Fantastic." Westfield Mall The fifth project collaboration between Dahua, KITT Engineering, and Ocean Outdoor is an LED display screen in Westfield Mall in the Netherlands. 24/7 remote system monitoring In addition to the regular LED screen and the driving system, a screen control and monitoring system was also developed to monitor the primary system at every point. “We want to see remotely how our assets in the country are doing," Fred explains. From the video player to dysfunctional LEDs, everything can be monitored remotely. For instance, it prevents the light intensity from being too high. Something that can have major consequences in outdoor advertising.
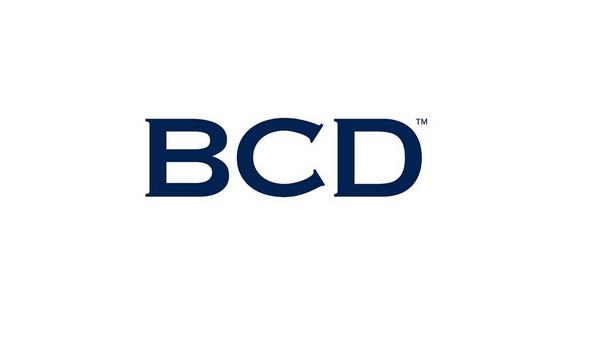
Like any retail franchise, car dealerships that have multiple locations nationwide require comprehensive, reliable, and scalable video surveillance solutions to protect their businesses. With dealership theft increasing by 7% since 2021, protecting high-value inventory, mitigating liability risks, and ensuring compliance with video data retention standards have become critical priorities. Future surveillance solutions BCD is vital to guarding functions, protecting valuable assets, and maintaining peace of mind Additionally, managing surveillance across multiple sites demands systems that are easy to deploy, cyber-hardened, and capable of centralised oversight. As dealerships continue to expand, investing in future-ready surveillance solutions with a trusted systems builder like BCD is essential to safeguarding operations, protecting valuable assets, and maintaining peace of mind. The challenge Car dealerships face distinct challenges when it comes to security and operations, such as: Asset Protection: Showrooms and lots house high-value vehicles and parts, making them prime targets for theft and vandalism. Cybersecurity Threats: Surveillance systems needed to be cyber-hardened to prevent breaches that could compromise sensitive footage or customer information. Reliable Recording: Continuous operation is essential to ensure no gaps in security coverage, particularly during off-hours or high-traffic events. Scalable Storage Across Locations: With multiple sites generating large volumes of video footage, dealerships need a solution to store data for 30-90 days to comply with industry regulations and internal policies. Centralised Management: Managing surveillance across dozens of locations required a solution that simplified oversight while enabling scalability for future growth. The solution BCD’s All-in-One Hybrid Cloud NVR is a cutting-edge video surveillance solution designed to address these challenges. The solution offers: Integrated PoE Switch: The All-in-One NVR includes a built-in Power over Ethernet (PoE) switch, simplifying installation and reducing the need for additional network infrastructure, which saves time and costs while simplifying the overall infrastructure. Cyber-Hardened Security: BCD’s solutions are all certified as cyber-hardened solutions to maximise data protection and minimise the risk of data breaches. Always-On Recording: With features like RAID storage for redundancy and failover capabilities, along with the Harmonise Remote Monitoring and Management plugin, the All-in-One solution ensures uninterrupted recording, and with customised notifications, can mitigate hardware or network disruptions. Hybrid Cloud Architecture: The All-in-One NVR provides 80TB of local storage for immediate access to live footage while seamlessly integrating with cloud storage for long-term retention. This hybrid approach ensures franchises can store footage for 30 days or more without overwhelming local resources. Centralised, Scalable Management: BCD’s solution is simple to deploy and typically takes 30 minutes or less, allowing franchises to monitor and manage surveillance across all locations from a single interface, simplifying administration and reducing operational overhead. The results Deploying BCD’s All-in-One Hybrid Cloud solution has the potential to drive significant improvements across multiple aspects of a franchise’s video surveillance operations, including: Enhanced Security: Reliable and cyber-hardened surveillance protect valuable inventory and reduce the risk of theft or vandalism. Continuous Uptime: The system’s failover mechanisms along with Harmonise Remote Monitoring and Management Plug-in ensures 24/7 recording with no interruptions, providing full coverage for liability and security events. Regulatory Compliance: Hybrid cloud storage allows each location to easily meet the 30-90-day retention requirement without costly local storage upgrades. Operational Efficiency: Centralized management and user-friendly tools reduce the complexity of overseeing surveillance across multiple locations, cutting costs and improving oversight. Future-Ready Scalability: As franchises expand, BCD’s solutions are designed to scale effortlessly to accommodate new locations and increased storage demands, providing a future-proof investment. Conclusion BCD’s All-in-One Hybrid Cloud NVR is an ideal solution for national franchises, such as car dealerships, and offers a secure, reliable, and scalable video data infrastructure. By leveraging hybrid cloud technology and simplified management, franchises will experience peace of mind knowing their assets are protected, compliance requirements are met, and their operations will be optimised for growth.
Global Security Exchange (GSX) 2025 news
ASIS International, the world’s largest association for security management professionals, has announced its programming lineup for Global Security Exchange (GSX) 2025 with in-per...